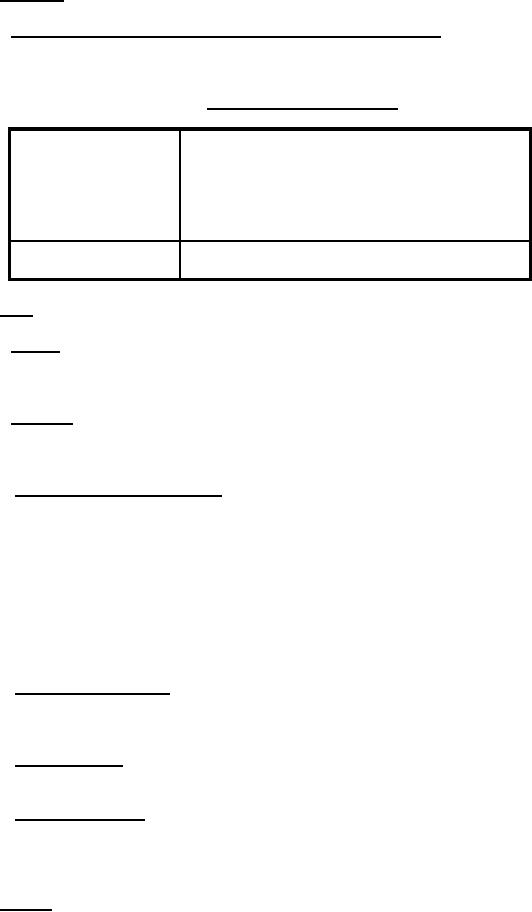
MIL-PRF-22344E
4.4 Inspection.
4.4.1 Examination of the end item for defects in appearance and dimensions. Each of the samples
selected shall be examined, weighed, and measured, as applicable, to determine conformance to the requirements
of 3.3 and 3.8. These tests shall be conducted on the actual lots to be shipped. Any unit containing one or more
visual or dimensional defects as shown in table II shall be cause for rejection of the unit.
TABLE II. Visual and dimensional defects.
Appearance:
Binder spots or foreign inclusions larger than 1 inch in
any two perpendicular dimensions. Delamination
larger than 4 square inches. Sections not slit or split
as ordered. Dents, depressions, or voids affecting
more than 10 percent of the surface face and 20
percent of the thickness.
Dimensions:
Not within limits or tolerances specified in 3.3.
4.5 Tests.
4.5.1 Density. Density of the pipe insulation shall be determined in accordance with the method
specified in ASTM C 302. On the jacketed product (see 6.3), density shall be determined by individual piece
weight, using nominal facing and adhesive weight.
4.5.2 Alkalinity. The alkalinity test shall be performed by the method 31 of ASTM C 169. A
representative sample may be prepared by taking borings using a large cork borer through the cross-section of the
pipe insulation.
4.5.3. Hydrogen-ion concentration (pH). The pH test shall be performed as follows: A 25-gram sample
shall be taken (a representative sample may be conveniently prepared by taking borings with a large cork borer
through the cross-section of the pipe insulation). A representative 1 gram specimen weighed to the nearest 0.001
gram shall be placed in a 500 mL Pyrex Erlenmeyer flask or equal, and 100 mL of distilled water added. The
distilled water shall be ASTM D 1193, Type I. Macerate the fibrous insulation with the flattened end of a
polyethylene stirring rod until the specimen is thoroughly wetted. Affix a 9 millimeter (mm) by 200-centimeter
(cm) Pyrex glass air condenser or equal, and set the flask on a hot plate. The hot plate shall be adjusted so that it
will maintain the contents of the flask at 194oF to 212oF, without boiling the water. The flask and contents shall be
heated for 1 hour after which time the flask shall be cooled to 68oF to 86oF. Transfer 50 mL of the extract to a
100 mL Pyrex glass beaker or equal, and measure the pH by ASTM E 70.
4.5.4. Hot surface performance. Hot surface performance of one sample of pipe insulation shall be
determined in accordance with ASTM C 411. Insulation for 1-inch pipe shall be tested at a temperature of 370oF,
and a thickness of 1 inch.
4.5.5. Fire performance. Three flat samples of pipe insulation shall be tested in accordance with MIL-
STD-1623.
4.5.6. Thermal conductivity. One sample of pipe insulation shall be tested in accordance with ASTM C
335. Determinations shall be made at three mean temperatures, 100oF, 150oF, and 200oF. Results of these tests
shall be extended, through reasonable curve fit or numerical techniques, to establish the thermal conductivity at the
levels specified in 3.7.
4.6 Toxicity. To determine conformance with the requirements of 3.9, the insulation shall be evaluated
using the HHA process. Sufficient data to permit a HHA of the product shall be provided by the
5
For Parts Inquires call Parts Hangar, Inc (727) 493-0744
© Copyright 2015 Integrated Publishing, Inc.
A Service Disabled Veteran Owned Small Business