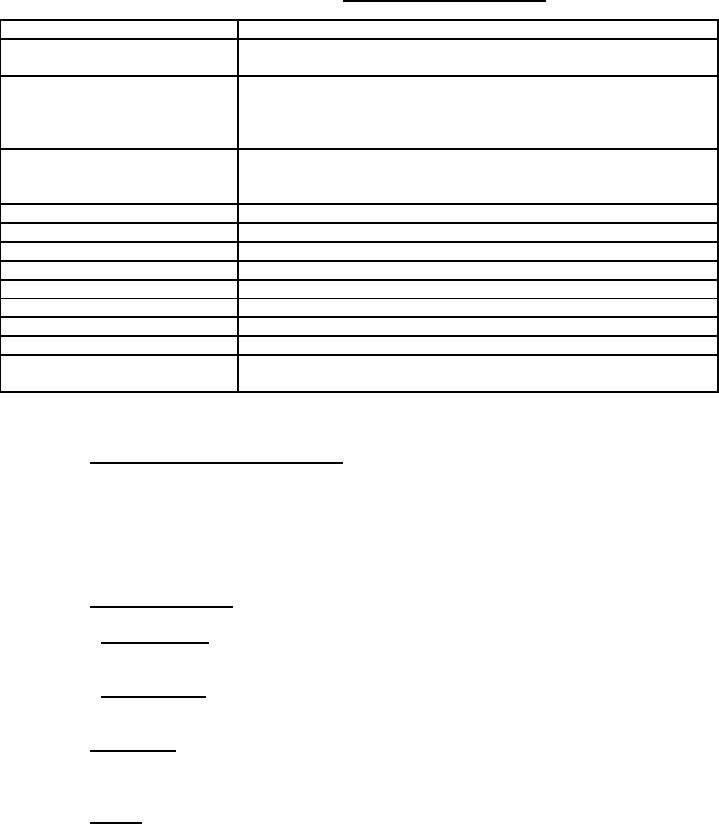
MIL-PRF-24172B (SH)
TABLE I. Type I and type II property values.
Inspection
Requirement
Density, apparent
Class 1 - 1.7 to 2.5 pounds per cubic foot
Class 2 - 2.5 to 4.0 pounds per cubic foot
Compressive strength at yield point Class 1 - Minimum of 20 lb/in2 in the direction of the rise
or 10 percent deflection
of the foam
Class 2 - Minimum of 40 lb/in2 in the direction of the rise
of the foam
Flame spread 25 (max)1
Fire resistance, droplets before
and after exposure to 4.5.10,
Smoke developed 250 (max)
specimen thickness 1 inch (nominal) No melting, dripping or flaming
Unicellularity
10 percent maximum open cells
0.16 Btu-in/hr ft 2 ºF maximum
Thermal conductivity (K factor)
Resistance to oil
No evidence of attack (softening, swelling or dissolving)
Heat aging
Maximum of 3 percent volume change
Humid aging
Maximum of 3 percent change in each linear dimension
Water absorption
0.08 pounds average per square foot of cut surface
Water vapor transmission
Maximum of 2.0 perm inches
Maximum of 40 lb/in2
Flexural strength
Low temperature aging
Maximum volume change of plus or minus (±) 4 percent
No cracking
1
Not to be construed as a fire hazard classification. Refers to test method only.
3.6 Dimensional form and tolerances (type I). The preformed board shall have dimensional uniformity with
square corners and sides, and ends shall be parallel. The length, width and thickness of the board shall be as specified (see
6.2) with the following tolerances:
Length - Plus 1/16 minus 0 inch per linear foot.
Width - Plus 1/16 minus 0 inch per linear foot
Thickness - Up to and including 2 inches, ± 1/32 inch. Greater than 2 inches, ± 1/16 inch.
3.7 Foam-in-place (type II). Prior to production, the foam system shall be tested as specified.
3.7.1 Cure temperature. The foam shall cure at ambient temperature as specified (see 6.2 and 6.3) and attain the
physical properties described herein within 48 hours after mixing.
3.7.2 Component ratio. The volume ratio between components for producing the required foam shall be a
maximum of five to one.
3.8 Workmanship. The preformed foam (type I) and the component ingredients for the foam-in-place (type II)
shall be processed in such a manner as to be uniform in quality and shall meet the requirements specified herein, as
applicable, and shall be free from other defects that will affect life, serviceability or appearance.
3.9 Toxicity. The insulation shall have no adverse effect on the health of personnel when used for its
intended purpose. The insulation shall be assessed by the Navy Environmental Health Center
(NAVENVIRHLTHCEN) using the administrative Health Hazard Assessment (HHA). A flowchart for this process
can be found as enclosure (1) of BUMEDINST 6270.8. The HHA is a review of the insulation based on
information submitted by the manufacturer, to assess health hazards associated with the handling, application, use
and removal of the product. The insulation shall not cause any environmental problems during waste disposal (see
4.6 and 6.6).
4
For Parts Inquires call Parts Hangar, Inc (727) 493-0744
© Copyright 2015 Integrated Publishing, Inc.
A Service Disabled Veteran Owned Small Business